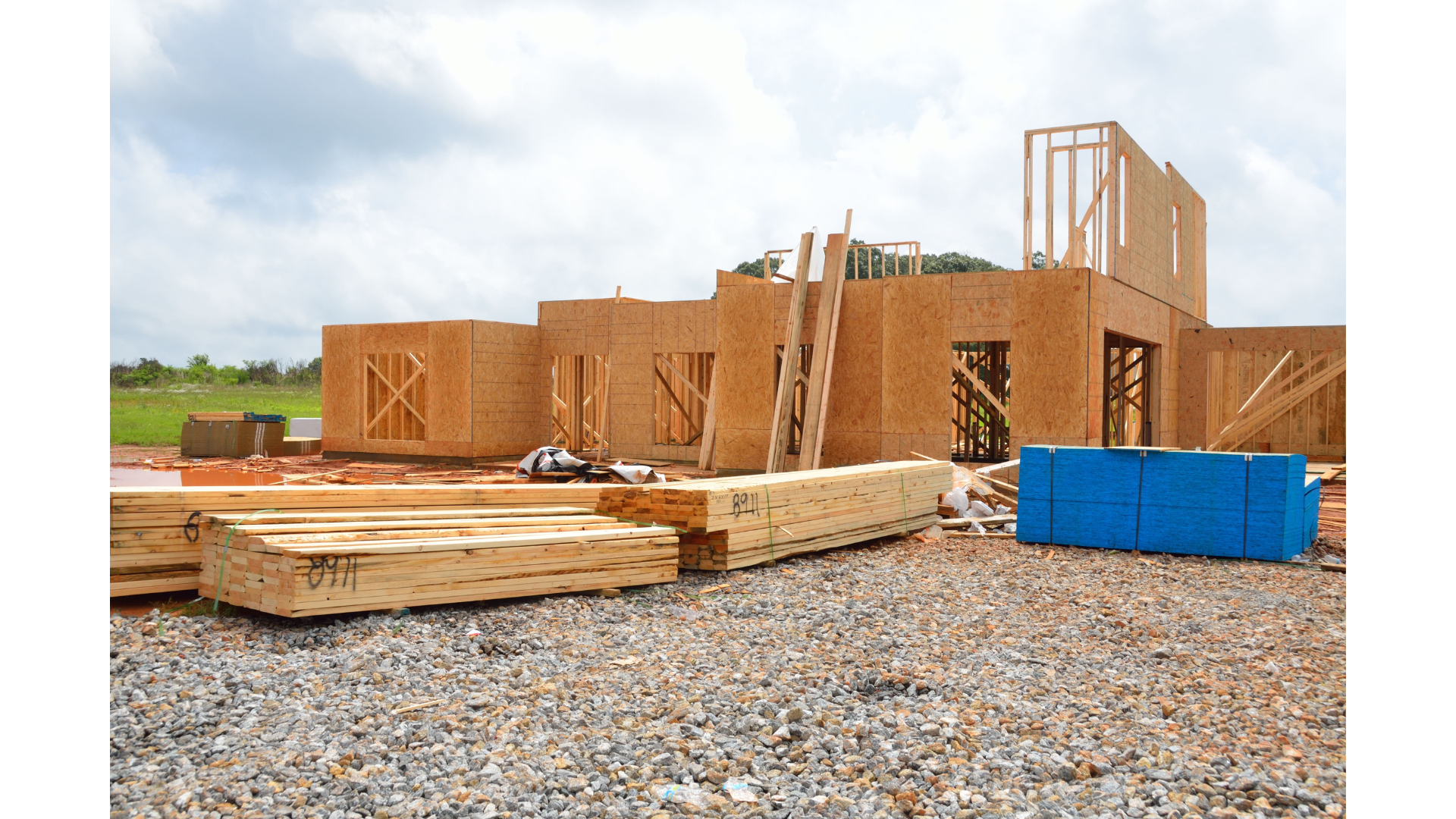
Custom Wear Solutions for Building Materials.
Discover why building material operations across North America trust Kalenborn to solve their toughest wear and abrasion problems.
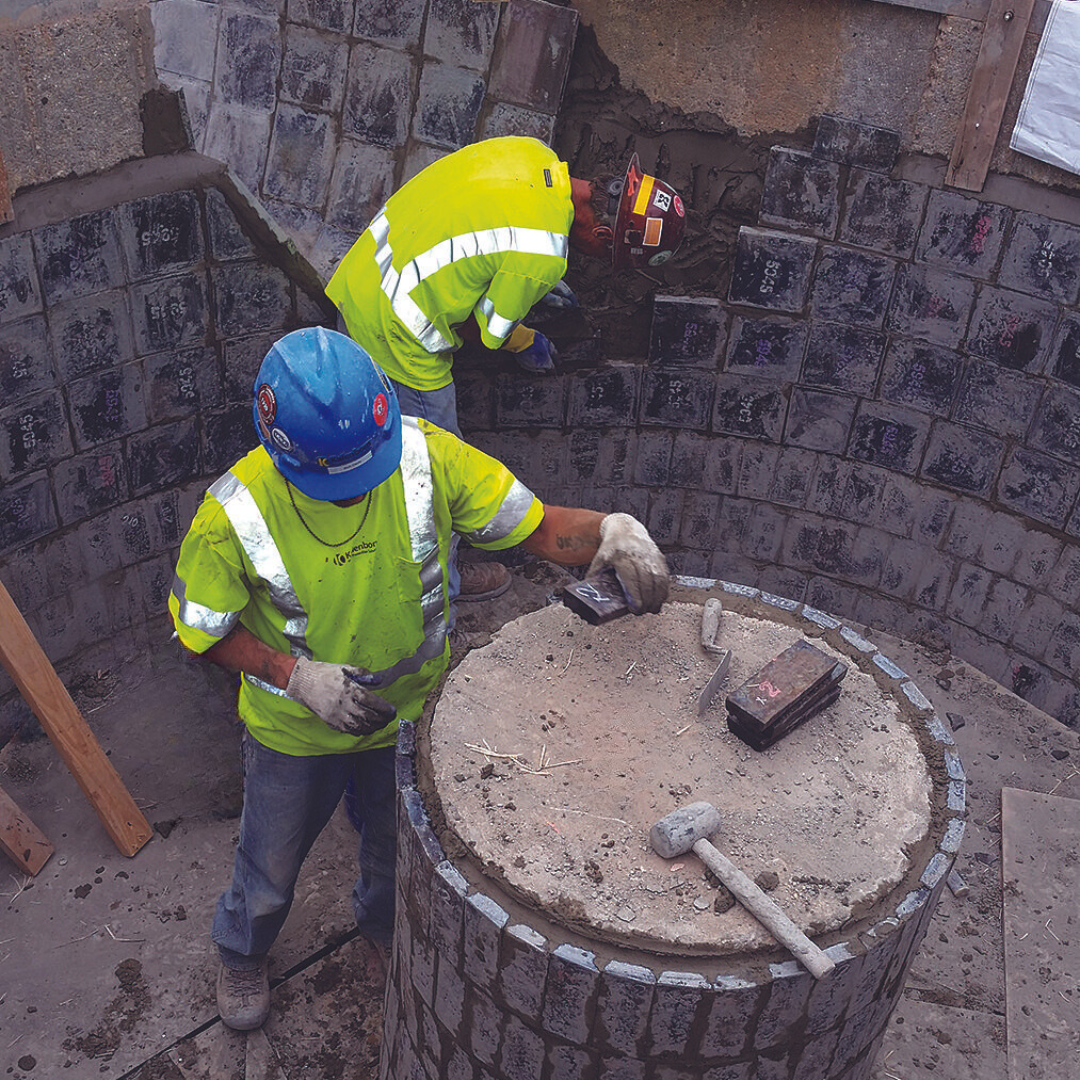
Why Kalenborn?
We are more than your vender. We are your engineering partner.
Conveying & Transporting
- Scrapper conveyor
- Screw conveyor
- Chutes, hoppers
- Fans
- Belt transfers points
- Pumps
- Walking floors
- Coke ramps
- Hydraulic piping
- Pneumatic piping
- Ducts
- Flumes
- Distributors
Crushing & Grinding
- Ball mills
- Vertical mills
- Crushers
- Crusher screen bars
Storage
- Tank
- Basin
- Tub
- Bunker
- Silo
- Loader Buckets
- Throughs
Mixing
- Disc mixer
- Double-shaft mixer
- Trommer mixer
- Drying plant
- Granulation plant
Filtering & Separating
- Cyclones
- Reactor cones
- Venturi
- Sifters
- Sieves
- Filter presses
- Dryers
- Separators
See how our solutions extend component life, reduce downtime, and improve uptime.
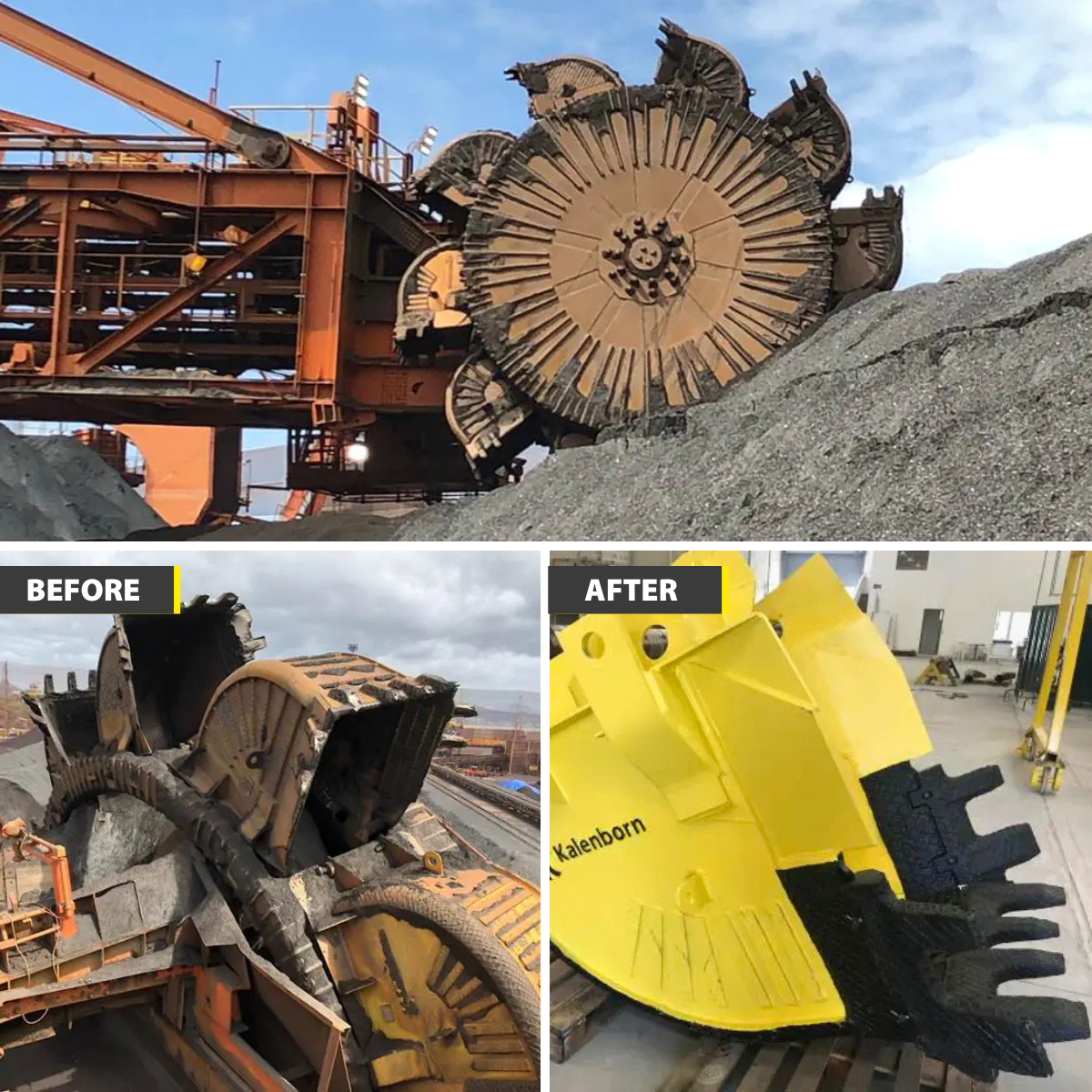
Bucket wheel reclaimer with impact-resistant bucket wheels for ore.
A long-time mining customer turned to Kalenborn for a more cost-effective wear protection solution. By combining KALMETALL W100 overlay plates and KALCAST hard cast materials, Kalenborn simplified the design, eliminated extra welding, and extended the service life of the bucket wheel reclaimer. The result: durable protection with reduced maintenance and downtime.
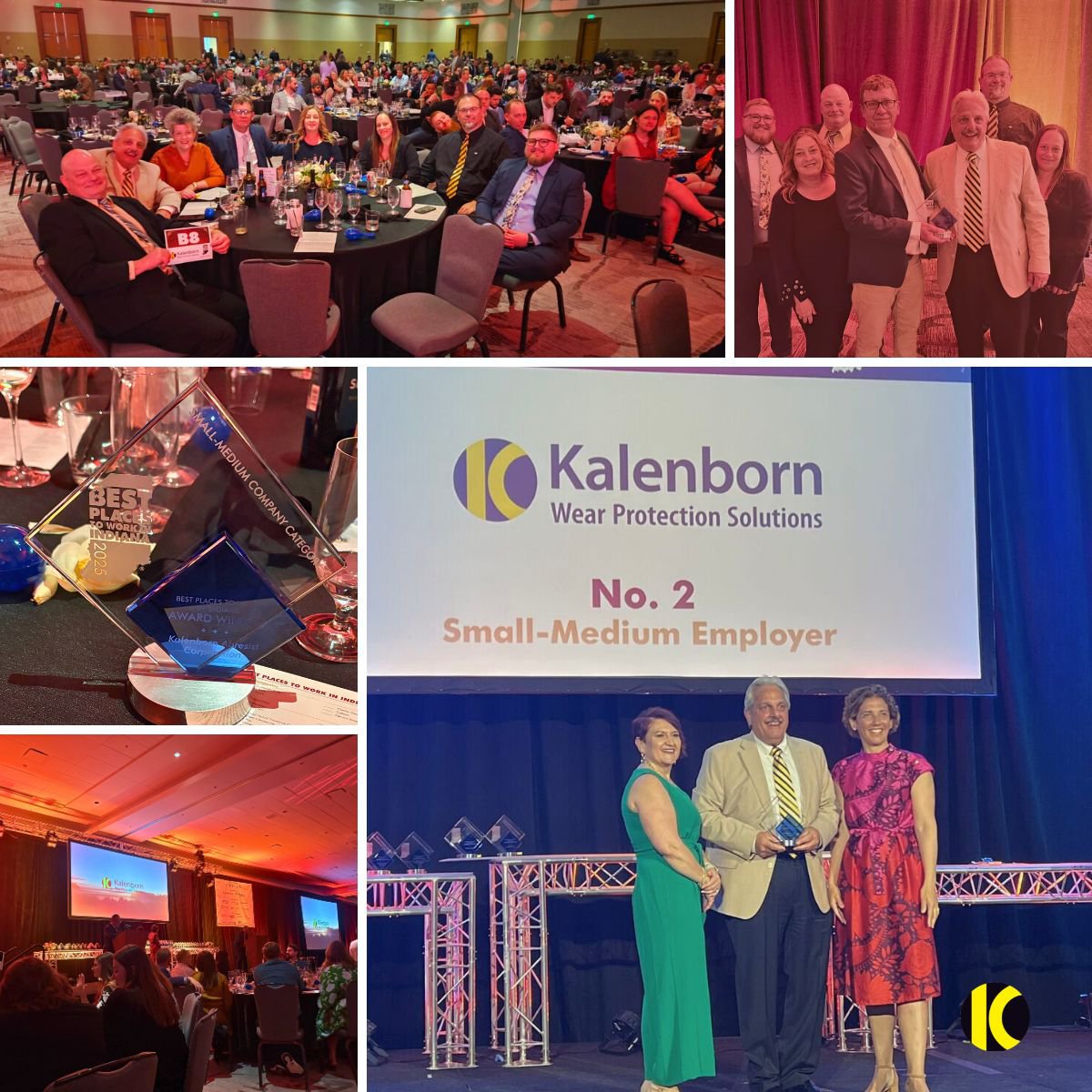
Kalenborn Named a Top Workplace in Indiana!
Kalenborn Abresist Corporation is proud to be recognized as the #2 Best Place to Work in Indiana (2025) in the small-medium business category by the Indiana Chamber of Commerce. This honor reflects our commitment to building a people-first culture where employee well-being drives our success. As a global leader in wear-resistant linings and corrosion protection, Kalenborn serves industries like mining, power, and steel with solutions that improve efficiency and equipment life. President Craig Frendewey sums it up best: “We are only as good as our people... this win is our report card from our team.”
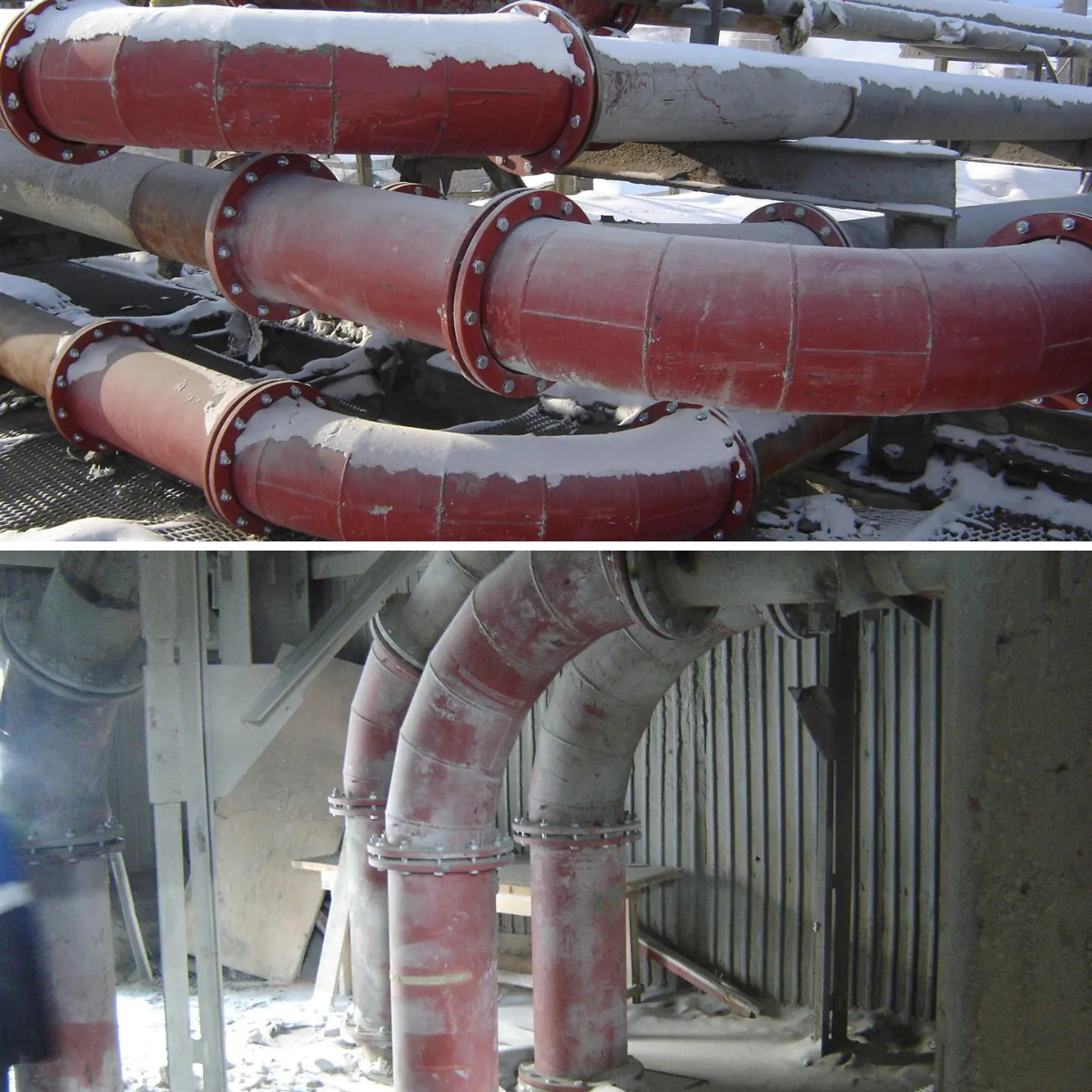
Higher performance with fused cast basalt ABRESIST pipes.
A cement plant struggled with frequent repairs, leaks, and high compressed air consumption due to thick-walled steel pneumatic pipelines. Kalenborn optimized the system by lining the pipes with ABRESIST fused cast basalt, significantly improving material flow, cutting compressed air use in half, and eliminating major wear for over a decade. The success has led to widespread adoption of ABRESIST in other plant areas and by additional cement facilities seeking efficiency and long-term savings.